Procurement planning can be difficult because of the number of different factors that must be considered. Assessing likely stock availability involves the significant task of combining the information from the supply and demand of existing orders, production forecasts, and planning suggestions.
At Fenwick, we have taken the availability tools that Dynamics NAV offers and restructured them to create the Item Availability Overview which makes it easier to estimate likely stock availability. This is part of the Fenwick Gold module Advanced Budgeting and Forecasting.
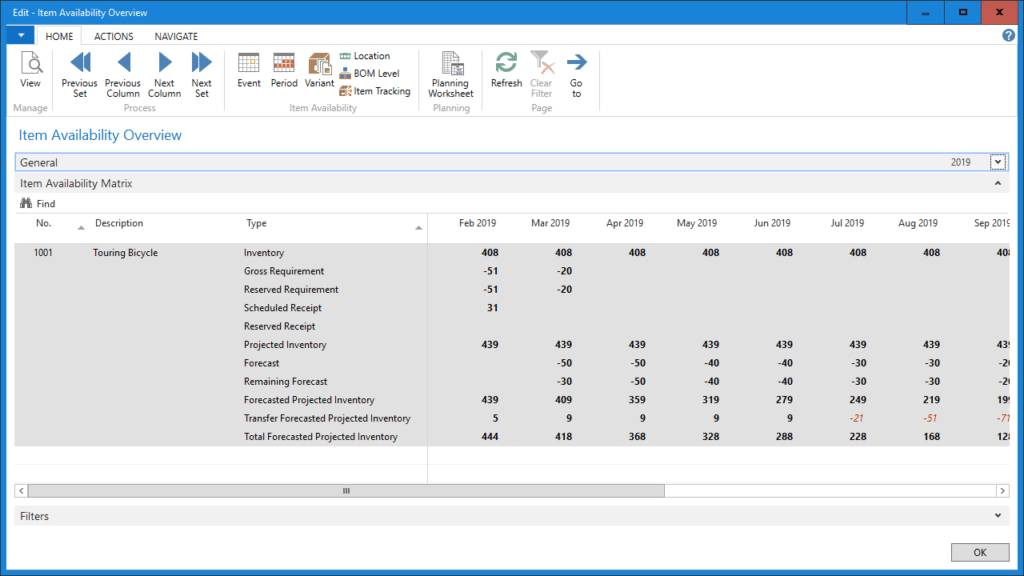
This reports key availability figures per period (Day, Week, Month, Quarter, Year, or Accounting Period).
Inventory – The current inventory for all Locations included in the Location Filter. If no Location Filter is set, the report will display the inventory for all Locations. This is the only value not to be reported by period as it is the current inventory.
Gross Requirement – The total demand in this Location(s). This includes all outgoing stock such as Sales Orders, Assembly and Production Consumption, Purchase Return Orders and Service Item Lines.
Reserved Requirement – The total demand in this Location(s) that is reserved to supply.
Scheduled Receipt – The total supply in this Location(s). This includes all incoming stock such as Purchase Orders, Assembly and Production Output and Sales Return Orders.
Reserved Receipt – The total supply in this Location(s) that is reserved to demand.
Projected Inventory – The expected availability of stock after considering existing stock (Inventory), all demand (Gross Requirement) and all supply (Scheduled Receipt).
Forecast – The forecasted quantity as per the Production Forecast that is selected in the Forecast Name field of the General tab.
Remaining Forecast – The forecasted quantity less the demand for that period. This value is used instead of the direct Forecast field so as not to over-report demand by recording the same values twice. That is, production forecast is intended as an estimation of what orders will be placed within a period and if some of those orders have already been placed, that should be considered when calculating the total available value.
Forecasted Projected Inventory – The projected inventory less the remaining forecast. If there is no inter-warehouse replenishment between locations, or there is only one location for the company, this can be considered the final value. It will appear orange if under Safety Stock and red if under zero.
Transfer Forecasted Projected Inventory – If this Item is replenished in other Locations from the Location being filtered to, this value will display the forecasted projected inventory of those locations. This is useful for providing a larger picture about where the stock is required and whether there will be enough available. It will appear orange if under the combined Safety Stock of those locations and red if under zero.
Total Forecasted Projected Inventory – This is the total of the forecasted projected inventory and transfer forecasted projected Inventory.
If the requisition or planning worksheet is being used, this can be considered by Including Planning Suggestions.
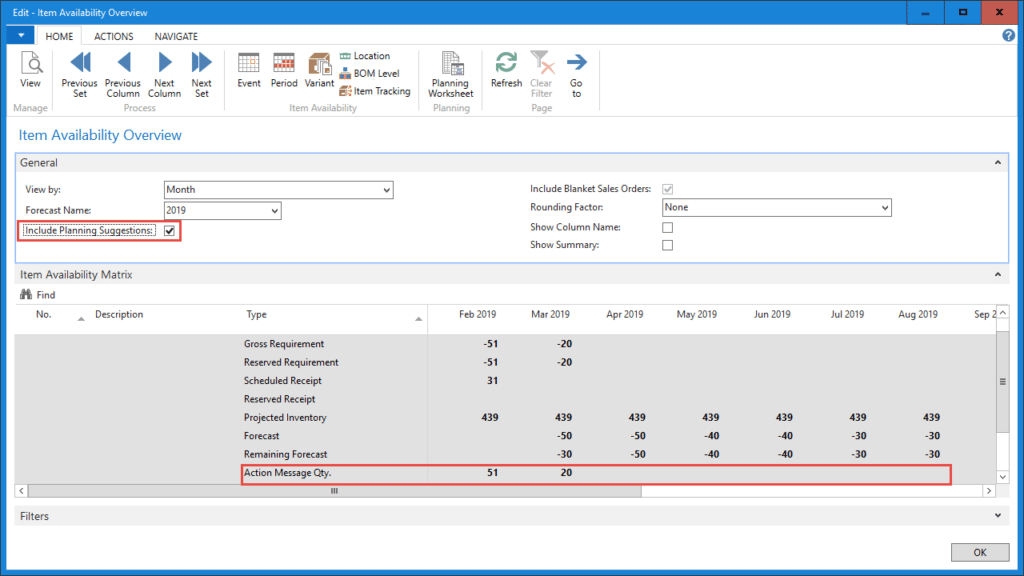
Action Qty. – The quantity suggested within the planning worksheet. The forecasted projected inventory values also change to suggested projected inventory values as they now consider the Action Qty.
A quick assessment of item availability can also be provided by Showing Summary and removing the Item Filter.
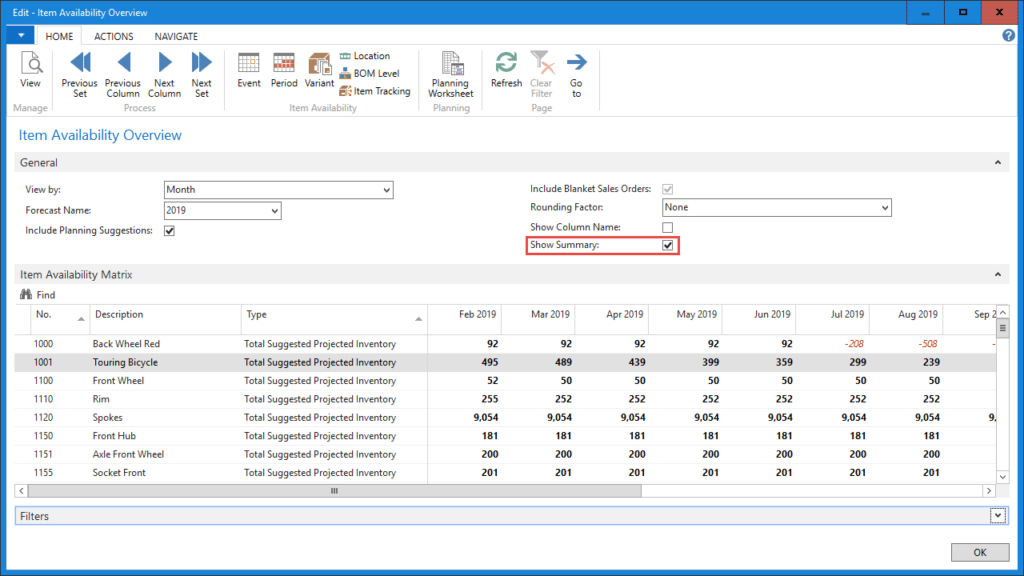
This tool was designed to assist procurement planners to accurately assess their stock levels so they can make informed decisions about ordering and scheduling. Alongside the replenishment planning capabilities of Dynamics NAV, planners should have complete visibility and control of their stock levels.