In today’s fast-paced logistics environment, warehouses face numerous challenges that impact efficiency and accuracy. Managing inventory, tracking movements, and ensuring timely order fulfillment can be challenging tasks, especially when relying on outdated methods. Overcoming warehouse obstacles with advanced handheld technology has become essential for businesses seeking to improve their operational efficiency.
In many warehouses, paper has been the go-to method for tracking inventory, managing orders, and documenting processes. But relying on paper comes with its own set of challenges—handwritten notes can be hard to read, documents can get lost, and manual data entry is time-consuming and error-prone.
Eliminating warehouse paperwork with advanced digital tools
Handheld technology has emerged as a transformative solution to these common warehouse challenges. By integrating advanced handheld devices into warehouse operations, businesses can overcome the limitations of traditional methods. These devices offer real-time data access, accurate inventory tracking, and streamlined processes, all from the palm of your hand.
By going digital, you’re not just improving accuracy—you’re also enhancing efficiency. With all the data captured and stored electronically, it’s easier to search, retrieve, and analyse information whenever needed. Plus, you’re contributing to a more sustainable environment by reducing paper waste.
Transforming warehouse operations with handheld technology
Over the years, we’ve successfully implemented numerous Microsoft Dynamics 365 Business Central warehouse solutions, enhancing operational efficiency for businesses. To address the growing need for mobility and real-time data access, we’ve taken our solutions a step further by implementing Mobile Warehouse Management System (WMS) by Tasklet Factory.
This advanced handheld solution complements the robust capabilities of Business Central, equipping warehouse teams with the tools needed to manage inventory, track movements, and handle critical tasks directly from their mobile devices. Instead of juggling clipboards and stacks of paperwork, your team can now use handheld devices to record, track, and manage inventory in real time. This shift not only streamlines operations but also reduces the risk of errors caused by illegible handwriting or misplaced documents.
Deep dive into key features and benefits
Managing warehouse inventory
Effective inventory management is critical in any warehouse. It’s not just about keeping track of what’s in stock—it’s about optimising every aspect of your operations. From maximising space utilisation to improving order fulfillment and boosting overall efficiency, proper inventory management is the backbone of a well-run warehouse. However, without the right technology, managing inventory can quickly become a cumbersome and time-consuming task.
Achieving accuracy within warehouse inventory
Accuracy is everything in the fast-paced world of warehouse management. That’s where Mobile WMS by Tasklet Factory comes in, offering a game-changing solution to eliminate guesswork and improve data management. Imagine saying goodbye to the days of scribbling on paper and hoping it’s legible later. With Mobile WMS, your team can enter information on the spot, right as they record it.
Mobile WMS takes accuracy a step further by incorporating barcode scanning, which significantly reduces the potential for errors. By scanning barcodes, your team can quickly and accurately capture crucial data—whether it’s product codes, shelf or bin locations, or even quantities. This ensures that all the necessary details are recorded with precision, leaving little room for mistakes that could disrupt your operations and helping avert warehouse challenges.
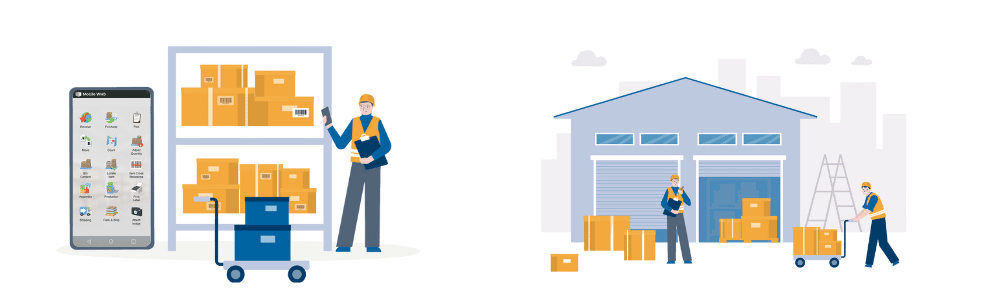
Streamlining operations with Mobile Warehouse Management solutions
One of the biggest challenges in warehouse management is dealing with stockouts. Mobile WMS helps you avoid these costly mistakes by providing real-time visibility into your inventory. With quick and accurate data, you can ensure that your stock levels are always up to date, preventing unnecessary disruptions in your supply chain.
Knowing exactly where each item is stored is crucial for maintaining efficiency. Mobile WMS offers instant location lookups, allowing your team to find items quickly and accurately. Whether it’s a busy day of order picking or restocking, this feature ensures that your team spends less time searching and more time getting the job done.
Additionally, moving items within the warehouse can be a challenging and complex process, especially when dealing with large volumes of stock. Mobile WMS simplifies this by streamlining item movements, making it easier to track and manage transfers between locations. This not only reduces the likelihood of errors but also speeds up the entire process, keeping your operations running smoothly.
Enhancing inventory accuracy with advanced stocktakes
With Mobile WMS by Tasklet Factory, your stocktake process becomes both efficient and reliable. Whether you’re conducting scheduled counts or need to perform a quick, unplanned audit, Mobile WMS has you covered.
Two main types of stocktake counts:
- Planned count: Based on your Physical Inventory Count, this method ensures thorough and accurate stocktakes. Conducted as a blind count by default, it requires users to physically verify and enter inventory details directly into the device, enhancing the integrity of your data.
- Unplanned count: Perfect for those unexpected moments when an immediate count is necessary. This ad-hoc option offers the flexibility to respond quickly to inventory discrepancies or sudden checks.
Your team can conduct stocktakes effortlessly as they move through the warehouse. Say goodbye to the outdated practice of tallying counts on paper and manually entering data into your ERP system. Instead, empower your staff to complete counts efficiently and accurately, directly on handheld devices.
Elevating warehouse management with digital tools
Making the switch from paper to digital with Mobile WMS simplifies your processes, increases productivity, and sets the stage for a more efficient and accurate warehouse operation. Using Mobile WMS by Tasklet Factory alongside Business Central solutions can truly transform your warehouse management.
Mobile Warehouse Management by Tasklet for Business Central effectively addresses common warehouse challenges like stockouts, quick location lookups, and item movements, all while eliminating the hassle of paper. By integrating this handheld technology, you’re setting your warehouse up for a smoother, more efficient operation. Embracing Mobile WMS means you’re investing in a smarter, more streamlined future for your warehouse, making everyday tasks easier and more reliable.