Availability by Item provides the user with a matrix style view of the state of inventory. From this page, filters can be placed to narrow down the search to easily find stock shortages based on the Projected Available Balance.
The Projected Available Balance is calculated using the following formula:
Inventory + Scheduled Receipts - Gross Requirements + Planned Order Receipt
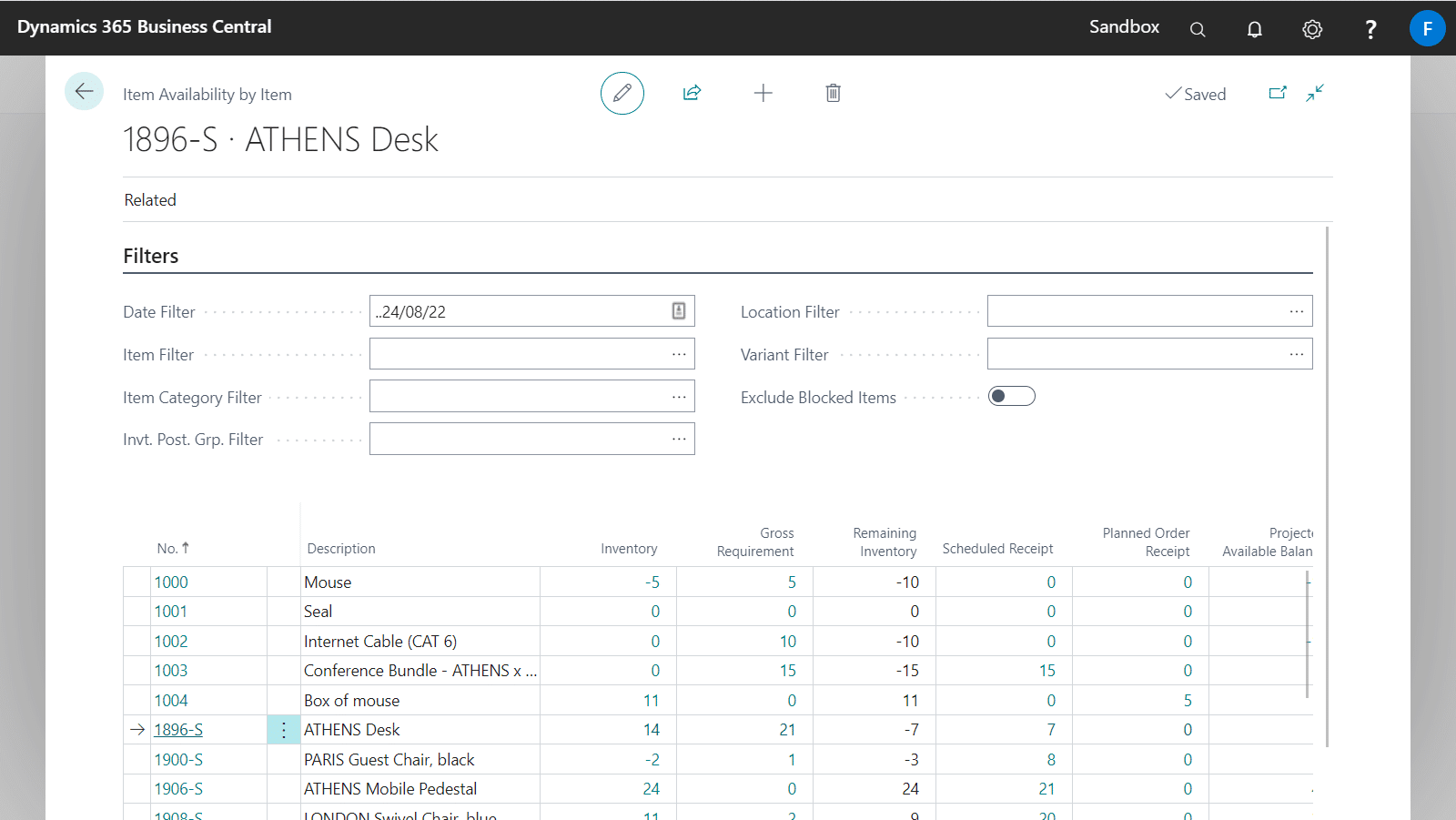
Fields visible by default:
Field | Description |
---|---|
No. | Specifies the item number. |
Description | Specifies the description of the item. |
Inventory | Specifies the inventory level of an item. |
Net Change | Specifies the net change in the inventory of the item during the period entered in the Date Filter field. |
Gross Requirement | Specifies the sum of the total demand for the item. The gross requirement consists of independent demand (which include sales orders, service orders and transfer orders) and dependent demand (which include production order components for planned, firm planned, and released production orders and requisition and planning worksheets lines). |
Remaining Inventory | Specifies the inventory level of an item less gross requirement. |
Scheduled Receipt | Specifies the sum of items from replenishment orders such as Purchase and Production orders. |
Planned Order Receipt | Specifies the item’s availability figures for the planned order receipt from Requisition and Planning Worksheet Lines. |
Projected Available Balance | Specifies the item’s availability. This quantity includes all known supply and demand but does not include anticipated demand from production forecasts or blanket sales orders. |
Fields that can be added using Personalise:
Field | Description |
---|---|
Qty. on Purch. Order | Specifies how many units of the item are inbound on purchase orders, meaning listed on outstanding purchase order lines. |
Qty. on Sales Order | Specifies how many units of the item are allocated to sales orders, meaning listed on outstanding sales orders lines. |
Qty. on Service Order | Specifies how many units of the item are allocated to service orders, meaning listed on outstanding service order lines. |
Qty. on Job Order | Specifies how many units of the item are allocated to jobs, meaning listed on outstanding job planning lines. The field is automatically updated based on the Remaining Qty. field in the Job Planning Lines window. |
Trans. Ord. Shipment (Qty.) | Specifies the quantity of the items that remains to be shipped. The program calculates this quantity as the difference between the Quantity and the Quantity Shipped fields. It automatically updates the field each time you either update the Quantity or Quantity Shipped field. |
Qty. in Transit | Specifies the quantity of the items that are currently in transit. |
Trans. Ord. Receipt (Qty.) | Specifies the quantity of the items that remain to be received but are not yet shipped. The program calculates this quantity as the difference between the Quantity and the Quantity Shipped fields. It automatically updates the field each time you either update the Quantity or Quantity Shipped field. |
Qty. on Asm. Comp. Lines | Specifies how many units of the item are allocated to assembly component orders. |
Qty. on Assembly Order | Specifies how many units of the item are allocated to assembly orders, which is how many are listed on outstanding assembly order headers. |
Expected Inventory | Specifies how many units of the assembly component are expected to be available for the current assembly order on the due date. |
Available Inventory | Specifies the quantity of the item that is currently in inventory and not reserved for other demand. |
Scheduled Receipt (Qty.) | Specifies how many units of the item are scheduled for production orders. The program automatically calculates and updates the contents of the field, using the Remaining Quantity field on production order lines. |
Schedule Issue (Qty.) | Specifies the sum of items from planned production orders. |
Planned Order Releases | Specifies the sum of items from replenishment order proposals, which include planned production orders and planning or requisition worksheets lines, which are calculated according to the starting date in the planning worksheet and production order or the order date in the requisition worksheet. This sum is not included in the projected available inventory. However, it shows which quantities should be converted from planned to scheduled receipts. |
Filters
Filter | Description |
---|---|
Date Filter | Specifies the dates that will be used to filter the quantities in the list. |
Item Filter | Specifies the item filter that will be applied to the list. |
Item Category Filter | Specifies the item category filter that will be applied to the list. |
Invt. Post. Grp. Filter | Specifies the inventory posting group filter that will be applied to the list |
Location Filter | Specifies the location filter will be used to filter the quantities in the list. |
Variant Filter | Specifies the item variant filter that will be used to filter the quantities in the list. |